
Шабер и осуществляемая посредством него операция, именуемая шабрением, используется для обеспечения плотного прилегания поверхностей сопрягаемых подробностей. Это достаточно трудоёмкая и специфичная слесарная операция, разрешающая довести (либо вернуть) сопрягаемые плоскости разных подробностей до идеала и тем самым достигнуть точности разных станков и оборудования, и обычного сопряжения трущихся между собой подробностей.
В данной статье, вычисленной больше на новичков, я весьма детально обрисую таковой инструмент как шабер, все его типы, его доводка и правильная заточка, и будет обрисовано, как грамотно произвести шабрение, припуски на шабрение, точность шабрения, контроль качества, шабрение направляющих станин станков и многие другие нюансы.
Для начала давайте разглядим какие конкретно бывают шаберы и для чего они используются.
Шабер — для чего он, какие конкретно они бывают и другие нюансы.
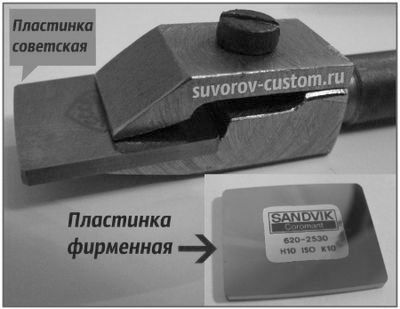
Посредством этого инструмента производится такая операция как шабрение, которая, как я уже сказал, используется для обеспечения плотного прилегания трущихся подробностей разных механизмов и станков. Шабрение, при умелых действиях, дает возможность приобрести точность поверхности от 0,003 до 0,01 мм (подробнее о ходе шабрения я напишу ниже).
За один проход посредством шабера возможно снять слой металла толщиной приблизительно 0,005 — 0,07 мм.
А при среднем давлении на инструмент, толщина снимаемого металла (стружки) в большинстве случаев не превышает 0,01-0,03 мм. При малом и чистовом шабрении давлении на инструмент, в большинстве случаев снимается тонкая стружка, толщиной всего 0,002 — 0,005 мм
По форме режущей части шаберы делятся на плоские, фасонные и трёхгранные. А по числу режущих кромок (граней) шаберы бывают односторонние и двухсторонние.
Ниже мы разглядим эти нюансы более детально, но прежде направляться заявить, что заводские шаберы изготавливают из углеродистой инструментальной стали марки У10А либо У12А. По окончании изготовления, их подвергают закалке до твёрдости HRC56-64.
Плоские шаберы. Самый распространены и их используют для шабрения плоских поверхностей (станин металорежущих станков и т.п.), открытых плоскостей, конечно разных пазов, других полостей и канавок, каковые не имеют криволинейных поверхностей.
Шаберы: а — плоский односторонний, б — с изогнутым финишем, в — двухсторонний (с плоским и закруглённым финишем), г — трёхгранный, д, е — фасонные (трёх и четырёхгранные).
В зависимости от числа режущих финишей плоские шаберы бывают двухсторонними и односторонними — с рукоятками на втором финише (см. рисунок 1) и двухсторонними.
Ответственные советы. направляться не забывать, что серьёзное значение имеет форма режущей кромки (лезвия) у шабера. Самый распространённой и рациональной есть мало выпуклая (полукруглая) форма лезвия (см. рисунок 1 в, и фото выше).
При заточке и изготовлении инструмента полукруглой режущей кромки, саму кромку (лезвие) рекомендую очерчивать и изготавливать с дугой радиуса приблизительно 30-40 мм — это если вы станете создавать получистовое шабрение.
Для чистового шабрения советую изготавливать (затачивать) полукруг лезвия с чуть бoльшим радиусом — приблизительно 40 — 55 мм.
Главное преимущество шаберов с полукруглой режущей кромкой, перед плоской режущей кромкой в том, что при отсутствии закругления у кромки лезвия, шабер в работе снимает металл всей плоскостью режущей кромки (всем лезвием) и от этого нужно будет применять большее упрочнение, но не это основное.
В противном случае, что в случае дефицита опыта и при мельчайшем отклонении (вправо-влево) плоской режущей кромки инструмента, острые углы плоского лезвия врезаются в металл и приводят к появлению глубоких царапин на обрабатываемой поверхности подробностей.
На полукруглой форме лезвия ещё и углы закруглены (это прекрасно видно на самом первом фото выше, где продемонстрированы закруглённые сменные пластинки) и таким инструментом нереально сделать глубокие царапины кроме того при недостаточном опыте, исходя из этого я советую новичкам трудиться лишь с полукруглой формой режущих пластинок.
Плоскую форму лезвия шабера рекомендуется применять лишь при неотёсанном шабрении, и наряду с этим рекомендую изготавливать режущее лезвие более широким, для уменьшения производительности возможности и повышения труда отклонить инструмент вправо-влево (конечно же в случае если поверхность имеет громадную площадь и разрешает подлезть более широкому инструменту).
А при получистовом шабрении ширину лезвия уменьшают, а вдруг не хватает опыта (либо при чистовом шабрении), оптимальнее применять шаберы с полукруглой заточкой, либо с односторонней радиусной заточкой (см. рисунок 1).
Трёхгранные и фасонные шаберы.
Данный инструмент (см. рисунок 1 г,д,е, конечно рисунок 2 в, г) изготавливают прямыми и изогнутыми и используются они как правило для шабрения криволинейных поверхностей, ну к примеру отверстий в подшипниках скольжения (вкладышей — об этом ниже) и других подробностей, каковые не имеют плоских поверхностей.
фасонные и составные шаберы : А — составной плоский, Б — трёхгранный прямой, В — трёхгранный изогнутый, Г — фасонный.
Отличия каждого инструмента прекрасно видны, в случае если взглянуть с его торца и с боку (см. рисунок 1 и 2).
Фасонные шаберы ещё бывают в виде металлических закалённых пластинок (и сменных также), каковые закреплены посредством гайки на финише стержня с рукояткой (рисунок 2 г).
А размеры и форма режущей пластинки для того чтобы инструмента (см. рисунок 2 г) конечно же зависит от формы и размеров фасонных поверхностей, каковые подлежат шабрению.
Составные шаберы. Они в большинстве случаев отличаются меньшим весом, по сравнению с другими типами шаберов. К примеру плоский шабер длиной 40 см имеет вес чуть больше 450 грамм, а составной шабер при длине в 60 см весит приблизительно 350 — 370 грамм.
Форма режущей части у составных шаберов не редкость плоской (см. рисунок 2) трёхгранной прямой и трёхгранной изогнутой (и двухгранной также). направляться подчернуть, что составные шаберы отличаются громадной чувствительностью, прекрасно пружинят (имеют хорошую упругость) и исходя из этого ими комфортно трудиться и регулировать толщину снимаемого слоя металла.
Шаберы- кольца (кольцевые). Эти инструменты изготавливают из обойм изношенных конических роликовых подшипников, при помощи заточки их на шлифовальных кругах (позиция А на рисунке 3) и потом доводят их торец на мелкозернистом либо алмазном круге (позиция Б на рисунке 3).
шаберы-кольца: А — заточка на точильном станке, Б- доводка, Г — шабрение вкладыша кольцевым шабером.
Используют их в большинстве случаев для шабрения вкладышей — позиция В на рисунке 3 (о шабрении вкладышей ниже) и для других криволинейных поверхностей.
Шаберы со сменными режущими пластинками. Это на данный момент самый распространённые инструменты из-за их преимуществ и удобства перед такой тип и другими типами продемонстрирован на самом верхнем фото и на рисунке 4 ниже. Главное преимущество — это конечно же возможность стремительной смены режущих пластинок, каковые изготавливают из разных жёстких сплавов.
Составные шаберы (со сменной пластинкой) l — главные части шабера, ll и lll — методы крепления пластинок.
А возможность стремительной смены пластинок разрешает подобрать инструмент (в зависимости от формы пластинки) фактически для задач и всех целей и для различных обрабатываемых поверхностей. К тому же при затуплении пластинки её неизменно возможно заменить, в случае если до тех пор пока нет заточного станка.
Ну и ещё один важный довод пребывает в том, что пластинку нужной формы несложно изготовить самостоятельно, к примеру из какой то ветхой дисковой фрезы, ножовочного полотна и других аналогичных (плоских) инструментов, изготовленных из быстрорежущей стали либо жёстких сплавов.
Но на данный момент уже возможно приобрести и качественные заводские пластинки от зарубежных компаний (см. самое первое фото вверху) либо отыскать советские пластинки, хорошего качества.
Инструмент для шабрения со сменными режущими пластинками и методы закрепления этих пластинок продемонстрированы на рисунке 4 (и самом верхнем фото).
Шабер с радиусной заточкой. Таковой инструмент продемонстрирован на рисунке 5 а, и главное отличие его от других типов в том, что режущая часть 1 затачивается по некоему радиусу, что значительно облегчает шабрение, поскольку таковой инструмент требует приложения намного меньших упрочнений (чем при шабрении плоским шабером).
Шабер с радиусной заточкой и дисковый шабер
Радиус закругления делаем приблизительно 30 — 40 мм для предварительного шабрения, и 40 — 55 мм для окончательного.
Дисковый шабер продемонстрирован на рисунке 5б и как видно в том месте, режущая часть у для того чтобы инструмента выполнена в виде металлического диска из закалённой (либо быстрорежущей) стали. Таковой инструмент используется для шабрения широких плоскостей и его возможно изготовить самостоятельно из маленькой дисковой фрезы, в случае если сточить её зубья и после этого довести кромку диска на заточном станке.
Диск имеет наружный диаметр приблизительно 50-60 мм, при толщине 3-4 мм и в большинстве случаев крепится посредством гайки 2 к концу стержня 3 инструмента. А при затупления режущей кромки инструмента, направляться всего лишь мало провернуть диск, ослабив гайку 2, после этого зажать её и возможно продолжать работу не затупившимся участком. Очевидно, в то время, когда затупится вся режущая кромка диска, то его снимают и создают заточку на круглошлифовальном станке.
доводка и Заточка шаберов.
Заточку этого инструмента создают на заточных станках (о станках детально вот тут) и кто знаком с доводкой и заточкой токарных резцов (о заточке резцов детально вот тут) то без неприятностей сможет заточить фактически любой шабер. В этом деле принципиально важно верно выбрать угол заточки и заточить под нужным углом режущие грани инструмента.
А углы заточки режущих граней (кромок) направляться выбирать в зависимости от материала обрабатываемых подробностей, и от характера работ.
Режущими кромками плоских шаберов являются их торцовые рёбра. На рисунке 6 продемонстрированы углы заточки плоского шабера в зависимости от обрабатываемого материала, и в том месте указаны углы (углы установки), под которыми направляться держать инструмент при работе.
его установки доводка и Углы шабера:
а — доводка торца шабера, б — доводка боковой поверхности шабера;
Углы заточки шабера для шабрения: в — бронзы и чугуна, г — стали, д — мягких сплавов.
Так для шабрения подробностей из бронзы и чугуна угол заточки равен 90-100°, для шабрения стали в большинстве случаев делают угол заточки равным 75 — 90° (чем мягче сталь, тем угол меньше), ну а для шабрения подробностей из мягких металлов угол заточки образовывает всего 35-40°.
Не считая рисунка 6, рекомендуемые углы заточки, в зависимости от обрабатываемого материала, продемонстрированы в таблице. Помимо этого, в том месте указаны углы заточки трёхгранных шаберов, и указаны углы установки инструмента при работе и углы резания.
Самый распространена заточка инструмента под углом заострения в 90°, так как по большей части шабрение применяют для восстановления направляющих металлорежущих станков, у которых направляющие изготовлены из чугуна.
При угле заточки в 90° и установки инструмента под углом 15-25?, угол резания будет составлять приблизительно 105-125?.
При таком угле резания инструмент достаточно легко снимает металл и наряду с этим не через чур врезается в него, ну и не проскальзывает. Ну и как я уже сказал, самый распространённой и рациональной формой заточки лезвия есть радиусная форма.
ТАБЛИЦА рекомендуемых углов режущей части плоских и трёхгранных шаберов.
Угол установки инструмента возможно и намного больше(75-80°) при работе способом на себя, но об этом подробнее ниже, в разделе «практика шабрения».
доводки шаберов и Практика заточки.
Как было сообщено выше, заточку режущих поверхностей инструмента создают на заточных станках, шлифовальным кругом (о заточных станках и о разных шлифовальных кругах ссылка выше). У плоских шаберов направляться сперва затачивать боковые грани, и лишь затем затачивают торцовую поверхность инструмента.
Ну и затем выполняется доводка, которая осуществляется вручную на чугунной плите, покрытой небольшим абразивным порошком либо пастой.
При доводочных операциях инструмент ставят в строго вертикальное положение (см. рисунок 6а выше) и сперва доводят (заправляют) торцовую режущую грань (двигая грань инструмента по плите вперёд-назад, с маленьким нажимом), наряду с этим принципиально важно держать инструмент строго вертикально. Ну а по окончании уже доводят боковые грани (см. рисунок 6б) двигая инструмент по чугунной плите вправо-влево (указано стрелкой на рисунке).
В случае если создавать доводку инструмента в последовательности, обрисованной мной выше, то это разрешит взять самые острые грани режущей кромки, наряду с этим на инструменте не будет завалов от доводки торцовой грани. При интенсивной работе заправку (правку, доводку) шаберов в большинстве случаев нужно заново создавать через несколько часов интенсивной работы.
А по окончании четырёх либо пяти заправок инструмент нужно заново заточить и довести. Не смотря на то, что это конечно же приблизительные эти и всё зависит от твёрдости и качества материала режущей пластинки инструмента, ну и от твёрдости обрабатываемой подробности.
Процесс шабрения, контроль и точность качества.
Шабрение — это окончательная отделочная обработка поверхностей подробностей, посредством соскабливания (снятия) с нужных участков тонкого слоя материала, посредством шабера, детально обрисованного выше. Шабрение используется в тех случаях, в то время, когда необходимо обеспечить весьма правильное соприкосновение поверхностей трущихся подробностей и взять плотное прилегание поверхностей сопрягаемых подробностей, ну и придать подробностям размеры и точные формы.
Эта операция довольно часто употребляется для восстановления плотного прилегания трущихся поверхностей подробностей металлорежущих станков (к примеру направляющих станины и суппорта) и восстановления точности под изношенных станков.
Припуски на шабрение должны быть маленькими, поскольку было сообщено выше, в ходе шабрения инструментом снимается тонкая стружка, толщиной всего 0,002 — 0,005 мм. Ну и конечно же припуски зависят от длины и ширины обрабатываемой поверхности (либо от длины и диаметра обрабатываемого отверстия).
Ниже приведены величины припусков на шабрение в миллиметрах, в зависимости от длины и ширины отверстий и плоскостей:
Ширина обрабатываемой поверхности — до 100 мм, а протяженность — от 100 до 500 мм —припуск образовывает 0,10 мм. Ширина обрабатываемой поверхности- до 100 мм, а протяженность — от 500 до 1000 мм — припуск образовывает 0,15 мм. Ширина обрабатываемой поверхности- до 100 мм, а протяженность — от 1000 до 2000 мм — припуск образовывает 0,15 мм. Ширина обрабатываемой поверхности- до 100 мм, а протяженность — от 2000 до 4000 мм — припуск образовывает 0,15 мм. Ширина обрабатываемой поверхности- до 100 мм, а протяженность — от 4000 до 6000 мм — припуск образовывает 0,15 мм.
Ширина обрабатываемой поверхности- 100 -500 мм, а протяженность — от 100 до 500 мм — припуск образовывает 0,15 мм. Ширина обрабатываемой поверхности- 100 -500 мм, а протяженность — от 500 до 1000 мм — припуск образовывает 0,20 мм. Ширина обрабатываемой поверхности- 100 -500 мм, а протяженность — от 1000 до 2000 мм — припуск образовывает 0,25 мм. Ширина обрабатываемой поверхности- 100 -500 мм, а протяженность — от 2000 до 4000 мм — припуск образовывает 0,30 мм. Ширина обрабатываемой поверхности- 100 -500 мм, а протяженность — от 4000 до 6000 мм — припуск образовывает 0,40 мм.
Ширина обрабатываемой поверхности- 500 -1000 мм, а протяженность — от 100 до 500 мм — припуск образовывает 0,18 мм. Ширина обрабатываемой поверхности- 500 -1000 мм, а протяженность — от 500 до 1000 мм — припуск образовывает 0,25 мм. Ширина обрабатываемой поверхности- 500 -1000 мм, а протяженность — от 1000 до 2000 мм — припуск образовывает 0,30 мм.
Ширина обрабатываемой поверхности- 500 -1000 мм, а протяженность — от 2000 до 4000 мм — припуск образовывает 0,45 мм. Ширина обрабатываемой поверхности- 500 -1000 мм, а протяженность — от 4000 до 6000 мм — припуск образовывает 0,50 мм.
Поверхности подробностей, предназначенных для шабрения заблаговременно подготавливают на строгальных, фрезерных либо шлифовальных станках, ну а поверхности малых подробностей опиливают вручную сперва большим (драчёвым), а после этого небольшим (личным) напильником.
Очевидно это не относится к поверхностям станков (направляющих суппортов и станин) каковые изнашиваются и их нужно вернуть посредством шабрения (на тему восстановления направляющих суппорта и станины станков я как нибудь напишу отдельную статью — статья уже написана и находится вот желающие и тут смогут кликнуть на ссылку и почитать). Не смотря на то, что кое-какие станки (их направляющие) восстанавливают сперва шлифованием, но конечно же всё зависит от степени выработки поверхностей и от возможностей ремонтной мастерской.
Перед шабрением поверхности ещё необходимо обработать (снять) острые кромки, по всему периметру обрабатываемой поверхности подробности. Потом потребуется поверочная плита, которая шепетильно протирается чистой ветошью и после этого на неё наносится равномерный узкий слой краски, которая является смесью порошка и моторного масла сажи либо лазури (берлинская лазурь), каковые направляться измельчить так, что бы между пальцами по большому счету не ощущалось кроме того небольших зёрен (в качестве измельчителя возможно применять кофемолку).
Для получения ровного и равномерного слоя, подготовленную краску наносим посредством холщовой тряпки, причём краску наносим с внутренней стороны тряпки. И выступая через поры тряпки, краска при перемещении по поверхности плиты тряпки, покрывает плиту узким и равномерным слоем.
Сейчас направляться шепетильно очистить поверхность подробности чистой ветошью и наложить подробность на смазанную краской плиту. Ну и потом остаётся с лёгким нажимом на подробность, сделать два-три круговых перемещения по плите, по окончании чего с опаской отделить подробность от поверочной плиты и разглядеть поверхность подробности. Окрашенные пятна на поверхности подробности означают выступающие участки, каковые необходимо снять посредством шабрения.
Совершенно верно так же проверяются и сопрягаемые подробности станков, к примеру салазки суппортов и направляющие станин, лишь вместо плиты краской намазываем особую линейку, к примеру ШД — 630 (ГОСТ 8026) и прикладываем её на направляющие станины, по которым движется суппорт станка (либо намазываем краской одну из сопрягаемых плоскостей продольных и поперечных салазок суппорта). Как я уже сказал — эта темя для отдельной статьи и я её в обязательном порядке напишу (уже написал и ссылка на статью чуть выше), так как она достаточно актуальна.
Практика шабрения.
Сам процесс шабрения содержится в постепенном снятии металла с окрашенных мест (окрашенные места означают выпуклости, а не окрашенные — впадины). Для начала приступаем к так называемой «разбивке» громадных пятен, при которой сильными перемещениями шабера снимаем (соскабливаем) стружку с выпуклых (окрашенных) мест.
Потом поверхность подробности очищаем от стружки и снова производим диагностику на краску, обрисованную мной выше, и затем заново повторяем процесс шабрения, соскабливая металл с выпуклых мест.
А в то время, когда пятна на поверхности будут размешаться равномерно, заканчиваем «разбивку» и приступаем к повышению количества пятен , соскабливая снова появляющиеся (по окончании проверки на краску) окрашенные места.
Практика шабрения — а — установка шабера, б — шабрение на себя, в — проверка точности шабрения.
Очевидно, что каждое последующее снятие металла (стружки) будет содействовать уменьшению высоты неровностей, каковые будут делиться на пара менее высоких выпуклостей, а общее их количество будет с каждым разом возрастать, наряду с этим направление рабочего хода инструмента любой раз направляться изменять, но об этом чуть позднее.
В ходе шабрения шабер удерживаем правой рукой за ручку (если Вы правша), и устанавливаем его под нужным углом по отношению к обрабатываемой поверхности подробности (об углах, в зависимости от твёрдости материала, я написал выше и продемонстрировал на рисунке 6).
Ну а левой рукой нажимаем на инструмент (см. рисунок 7а) приблизительно чуть ниже его середины.
направляться приблизительно учесть, что давление рукоой на инструмент должно быть в пределах 2-5 кг, не более. Ну а при обратном (холостом) ходе назад, на инструмент не давим по большому счету. Ещё новичкам направляться учесть, что шабрение делают за пара переходов, а инструмент направляться двигать в различных направлениях так, дабы последующий движение (штрих) происходил с перекрытием прошлого.
Правильнее, дабы последующий штрих проходил под углом в 45 — 90 градусов к прошлому штриху. Так и появляется так называемый «холод» разной формы, другими словами симметрично расположенные риски (полосы) либо клеточки, ну либо ромбики (см. рисунок 7). Они так же содействуют удерживанию смазки на сопрягаемых между собой трущихся подробностях, что принципиально важно (так же принципиально важно как и риски от хона, удерживающие моторное масло на поверхности цилиндров двигателей). Сохраняю надежду с этим ясно новичкам, идём дальше.
При получистовом и чистовом шабрении оптимальнее использовать способ на себя, при котором шабер, имеющий длину приблизительно 45 — 55 см (время от времени и более — зависит от роста работника) обхватываем за среднюю часть обеими руками, а верхняя часть собственной рукояткой упирается в плечо работника. Наряду с этим стараемся расположить инструмент под углом в 75-80° по отношению к обрабатываемой поверхности.
При таком методе рабочим ходом инструмента есть перемещение лезвия на себя и при таком методе трудиться значительно эргономичнее, положение инструмента оказывается более устойчивым, соответственно улучшается уровень качества обработки и к тому же достигается более высокая производительность (приблизительно в 1,5 — 2 раза) если сравнивать с простым методом шабрения.
Ну и ещё важный момент — наряду с этим методе долгий шабер лучше пружинит, что снабжает плавное врезание лезвия и значительно бoльшую точность обработки.
Проверка качества шабрения.
Уровень качества контролируют сперва внешним осмотром, и пришабренная поверхность не должна иметь царапин и глубоких следов шабера. Ну а точность шабрения проверяется числом пятен, расположенных на площади квадрата, любая из сторон которого равна 25 мм.
В качестве квадрата используют особые рамочки (см. рисунок 7в) со сторонами равными 25 мм, каковые несложно вырезать самому.
Приложив рамочку к пришабренной поверхности, потом направляться посчитать количество пятен, находящихся в неё (в квадрата со сторонами 25 мм). Причём количество пятен на всей пришабренной поверхности определяют как среднее арифметическое значение, вычисленное из нескольких испытаний на различных участках всей поверхности подробности.
На площади, ограниченной рамкой 25х25 мм, для весьма неотёсанного шабрения достаточно добиться всего четырёх пятен; для неотёсанного шабрения достаточно девяти пятен; для правильного шабрения хватает 16 пятен; ну и для весьма правильного шабрения нужно добиться 20 — 25 пятен.
Правильное шабрение. При правильном шабрении не употребляется проверка на краску, а применяют в большинстве случаев неотёсанную либо среднюю полировальную пасту ГОИ (национальный оптический университет). По окончании одного либо двух проходов шабером по поверхности подробности, разводят посредством керосина полировальную пасту и наносят её на поверочную плиту. После этого на поверхность плиты уладывают подробность притираемой поверхностью и ведут притирку шабруемой поверхности до того момента, в то время, когда паста из зелёной превратится в тёмную и таковой процесс повторяют три либо четыре раза.
Затем шепетильно очистив поверхность подробности, осматривают поверхность, на которой показались блестящие пятна (каковые означают выпуклости) и остались более чёрные пятна, означающие впадины.
Сейчас необходимо снять посредством шабера блестящие пятна, и снова притереть поверхность пастой и повторить шабрение, пока не будет взята поверхность требуемого качества, которая определяется снова же посредством рамочки, размером 25х25 мм.
При вышеописанном методе (с применением пасты) направляться учесть ответственное событие: полировальная паста способна срабатывать не только поверхность подробности, но и поверхность поверочной плиты. Исходя из этого в обязательном порядке нужно, до и по окончании работы, шепетильно осуществлять контроль состояние поверхности поверочной плиты, к примеру посредством лекальной линейки (на просвет — о величине отклонения от прямолинейности делают выводы по размерам световой щели).
Не обращая внимания на выше описные хлопоты с проверкой состояния плиты, применение пасты ГОИ разрешает повысить производительность правильного шабрения в несколько раз.
Шабрение криволинейных поверхностей (вкладышей подшипников).
Шабрение криволинейных поверхностей, к примеру вкладышей подшипников скольжения, имеет кое-какие особенности. Во первых тут используют трёхгранные прямые либо изогнутые шаберы (о них написано выше), ну и во вторых имеются отличия в работе.
шабрение вкладышей: 1 — шабрение вкладыша полукруглым шабером, 2 — прозрачный целлулоидный шаблон сетка для проверки качества, 3 — шабрение фасонным трёхгранным шабером, 4 — шабрение кольцевым шабером.
Сперва наносят узкий и равномерный слой краски на участок вала, что будет соприкасаться с вкладышем. После этого окрашенный вал укладывают на нижний вкладыш (вкладыши) и потом равномерно (крест на крест) и с маленьким упрочнением затягивают крышку подшипника. Затягиваем гайки крышки до таковой степени, что бы вал возможно было провернуть с некоторым упрочнением вправо-влево, на пару-тройку оборотов.
Возможно на начальной стадии и не зажимать крышки подшипников, а просто укладывать вал в нижние вкладыши и мало прижав его, провернуть вправо влево на 2-3 оборота.
Затем откручиваем гайки и снимаем вал и крышку подшипника, и потом пришабриваем окрашенные места вкладыша (означающие выпуклости) перемещая инструмент по форме окружности вкладыша. Шабер наклоняем к поверхности вкладыша так, дабы снимала металл средняя часть режущей кромки инструмента.
Инструменту придают маленькое вращательное перемещение и наряду с этим в один момент прижимают к поверхности обрабатываемой подробности. Потом повторяем диагностику на шабрение и краску, пока не менее 3/4 площади поверхности вкладыша не будет равномерно покрыто пятнами краски.
Но более совершенно верно уровень качества шабрения возможно проверить в случае если вырезать из картона шаблон, в котором имеется всё то же окно 25х25 мм и приложить его (изогнув шаблон) к поверхности вкладыша.
В случае если вкладыш имеет громадной размер, то возможно изготовить шаблон из прозрачного пластика (целлулоида — продемонстрирован на рисунке чуть выше), на котором расчертить сетку, с ячейками снова же размером 25х25 мм.
Механизация шабрения. Шабрение есть достаточно трудоёмкой слесарно-подгоночной (доводочной) операцией. К примеру для шабрения чугунной поверхности площадью 2 квадратных метра, нужно затратить более 100 часов труда квалифицированного работника. Исходя из этого механизация таких работ на производстве имеет громадное значение.
Для механизированного шабрения используют разные особые приспособления, ускоряющие и облегчающие процесс шабрения. Это и пневматические шаберы, трудящиеся по принципу отбойного молотка от действия сжатого воздуха, и электро-механические инструменты, трудящиеся от электросети. У всех из них фактически одинаковый принцип работы — это преобразование электричества (либо энергии давления воздуха) в возвратно поступательное перемещение режущей пластинки шабера.
Но однако механическое шабрение подходит больше для объёмов работы и больших площадей на производстве. Исходя из этого детально я не буду обрисовывать его. Ну а ручной метод считается более правильным и аккуратным, ну и подходит он оптимальнее для гаражных их мастерских и мастеров.
Брак при шабрении и меры его предупреждения.
Вид брака: полное перекрытие краской пришабриваемойповерхности металла. Обстоятельство брака: нанесение на поверочную плиту (либо линейку) слишкомтолстого слоя краски.
Мера предупреждения: с опаской наносим краску (берлинскую лазурь) узким слоем. Вид брака: окрашивание края либо середины пришабриваемой поверхности. Обстоятельство брака: неверная предварительная обработка поверхности металла. Мера предупреждения: контролировать правильность предварительной обработки поверхности. Вид брака: наличие блестящих полос на пришабриваемой поверхности металла.
Обстоятельство брака: шабрение лишь в одном направлении. Мера предупреждения: производим шабрение в различных направлениях, что бы штрихи размешались под углами 45 — 60?. Вид брака: неравномерное размещение пятен на пришабриваемой поверхности. Обстоятельство брака: через чур сильный нажим на шабер, либо шабрение через чур долгими штрихами.
Мера предупреждения: при шабрении выполняем осторожность и не делаем сильный нажим на инструмент, конечно не делаем через чур долгие рабочие ходы инструмента. При черновом шабрении движение инструмента должен быть не более 10 — 15 мм, а при чистовом шабрении движение должен быть не более 5 — 10 мм. Вид брака: образование рисок на пришабриваемой поверхности металла. Обстоятельство брака: не качественная заправка (доводка) инструмента, либо наличие заусенцев на его кромках, ну либо попадание жёстких примесей в краску.
Мера предупреждения: контролируем состояние и качество заправки режущей кромки лезвия шабера. Потом контролируем его работу на ненужной подробности. Контролируем состав и качество краски, кстати, в случае если её наносить через тампон из мелко-пористой ткани, то возможность попадания жёстких частиц сводится к нулю. Вид брака: глубокие впадины на пришабриваемой поверхности. Обстоятельство брака: через чур сильный нажим на шабер.
Мера предупреждения: заблаговременно подготавливаем подробность к шабрению посредством чернового шабрения и предварительного опиливания с малыми просветами. При шабрении не очень сильно давим на инструмент и снимаем стружку маленькой толщины. Вид брака: наличие шероховатостей и заусенцев на пришабриваемой поверхности.
Обстоятельство брака: доводка шабера и неправильная заточка, конечно его неправильное перемещение при шабрении. Мера предупреждения: верно затачиваем и доводим инструмент, дабы исключить работу тупым лезвием, конечно читаем выше о правильных движениях и правильном пользовании инструмента. Вид брака: неточность пришабренной поверхности. Обстоятельство брака: использование неточного поверочного инструмента, либо неправильное пользование им, либо неправильное перемещение шабруемой подробности по поверочному инструменту (либо напротив инструмента по подробности) при проверке на краску. Мера предупреждения: вовремя контролируем точность (либо прямолинейность) поверочного инструмента, конечно содержим в чистоте рабочие поверхности поверхности деталей и поверочного инструмента.
Ну и не нажимаем очень сильно на поверочный инструмент при проверке на краску (верно пользуемся инструментом).
Вот помой-му и всё, в случае если ещё что то отыщу в памяти, то в обязательном порядке допишу. Надеюсь, что обрисованный тут инструмент — шабер, да и сам процесс шабрения, я обрисовал достаточно детально и данный материал будет нужен начинающим мастерам, удач всем.